Why businesses struggle with industrial asset lifecycle management
and how (good) software can reduce a major source of industrial waste
There is too much industrial waste
I have spent my entire career around the industrial world. Before Aucto, I ran a used equipment brokerage. At my last company, we would buy pre-owned and surplus industrial parts and machinery, and resell it for a profit. A big part of my job was to tour industrial facilities, kick the tires on used equipment and hopefully make some deals that made my firm a bunch of money. In this role, I got the unique opportunity to walk through, literally, thousands of industrial facilities- ranging from jet engine manufacturing plants to slaughter houses. What always struck me was the sheer amount of industrial machinery, parts and equipment that was sitting idle, no longer being used in operations. There was so much equipment available in fact, that I would typically buy unused, surplus equipment at about 2-3% of the original book value. My company started spinning up one huge warehouse after another to store our purchases- only to have them filled up in a matter of months. We just couldn’t keep up with the amount of surplus being generated by the manufacturing industry.
As it turns out, my grassroots perspective validated the existence of a huge problem with the way industrial supply chains operate. US businesses spent over 1 Trillion dollars last year on machinery and equipment. Experts believe that about 20% of a typical organization’s assets are surplus- which means Billions of dollars of surplus, obsolete or simply unused industrial assets are currently sitting in boneyards, warehouses and in tucked away corners of manufacturing sites. Some of these assets will get resold on the second market. The majority of them will ultimately end up in scrapyards and landfills. These assets make up a decent percentage of the 7.6 Billion tons of industrial waste generated each year, of which 70% ends up in landfills. The numbers are incomprehensibly large- but if you’re a supply chain professional, an asset manager or if you have spent enough time in manufacturing facilities- you have likely witnessed this cycle in action.
Waste is caused by friction, created by a lack of technology in asset lifecycle management
After a deep dive into how industrial supply chains work, I realized businesses are obsessed with hyper-optimizing their procurement processes. Vendors, ERP systems and tech startups have picked up on this obsession, and there seems to be endless technological innovation in making it easier, faster and cheaper to get more assets on your balance sheet. For example, this non-exhaustive market map of procurement tech companies demonstrates just how much technological advancement there has been in recent years in the procurement-tech space.
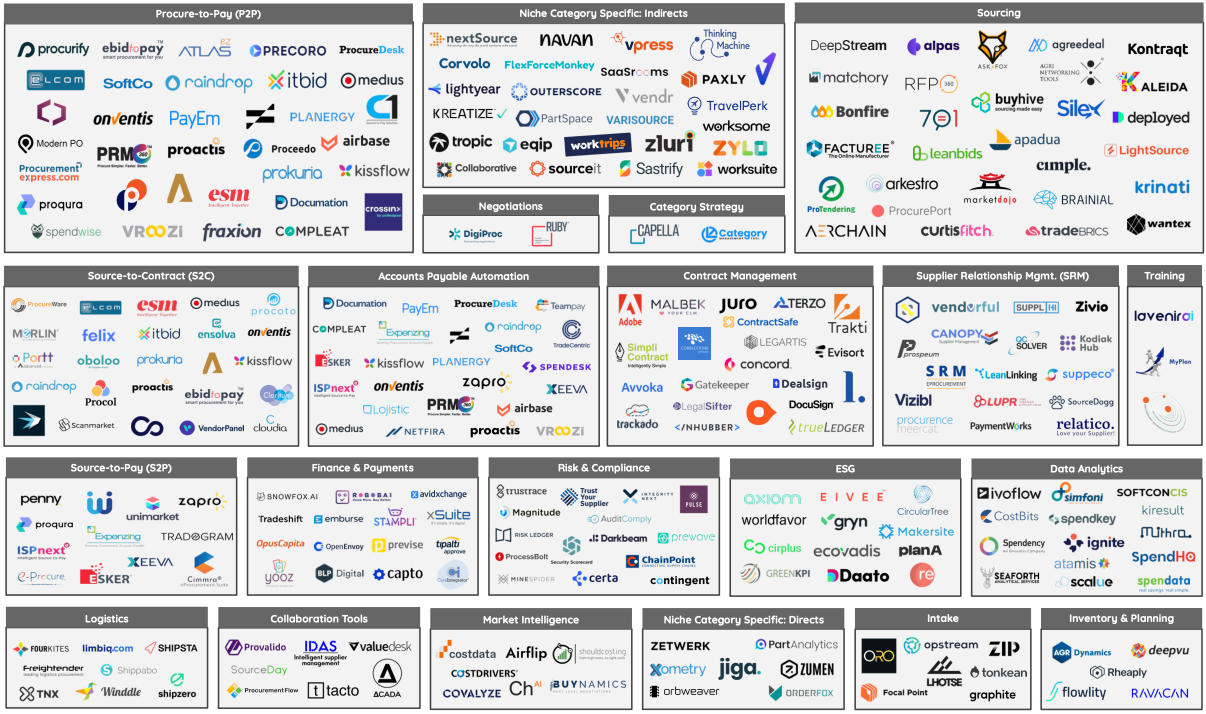
However, nobody seems to focus on what should happen to machinery and equipment once they are cycled out of production, or if they are no longer needed for operations. During the procurement process, no thought is given to:
- How do I track these assets throughout their lifecycle?
- When is the optimum time to cycle these assets out of operation?
- How should I be thinking about maximizing my return on these assets (outside of initial procurement costs and cost of ownership)?
- How do I ensure these assets don’t increase our environmental footprint?
And because businesses were not having these conversations with their supply chain and technology partners, no meaningful technology or solution was built to help businesses answer these questions.
So ultimately, without the right tooling, businesses revert to offline (and horribly inefficient) methods to try to manage their asset base. When comparing the efficiency at which an enterprises source and procure assets to how well they manage those assets throughout their lifecycle- the most appropriate analogy is going from a super highway to a dirt road. So it shouldn’t be a surprise that asset managers face incredible friction when it comes to identifying and managing underutilized assets- ultimately leading to increased waste.
Businesses want to solve this problem, but don’t know how to do it
This is not to say these businesses are intentionally wasteful. In fact, the mere existence of a $300 Billion dollar (and growing) industrial re-commerce market proves there is a real desire for businesses to seek better returns on their industrial assets. The financial motivation is certainly there. According to the CAPS Research benchmark study on investment recovery, the average enterprise resells approximately $8 Million dollars of surplus assets each year. That $8 Million goes straight to the bottom line, since there is almost no cost to generating this revenue.
Besides the financial motivation to fix this problem, ESG and compliance initiatives are also a driving force to reduce industrial waste. Recently, there seems to be a race to adopt circular economy initiatives as both investors and consumers demand sustainability from corporations. More than half of the largest companies in the world have signed up for net zero commitments- which should mean an increased focus on refurbishment, landfill divergence and resale programs.
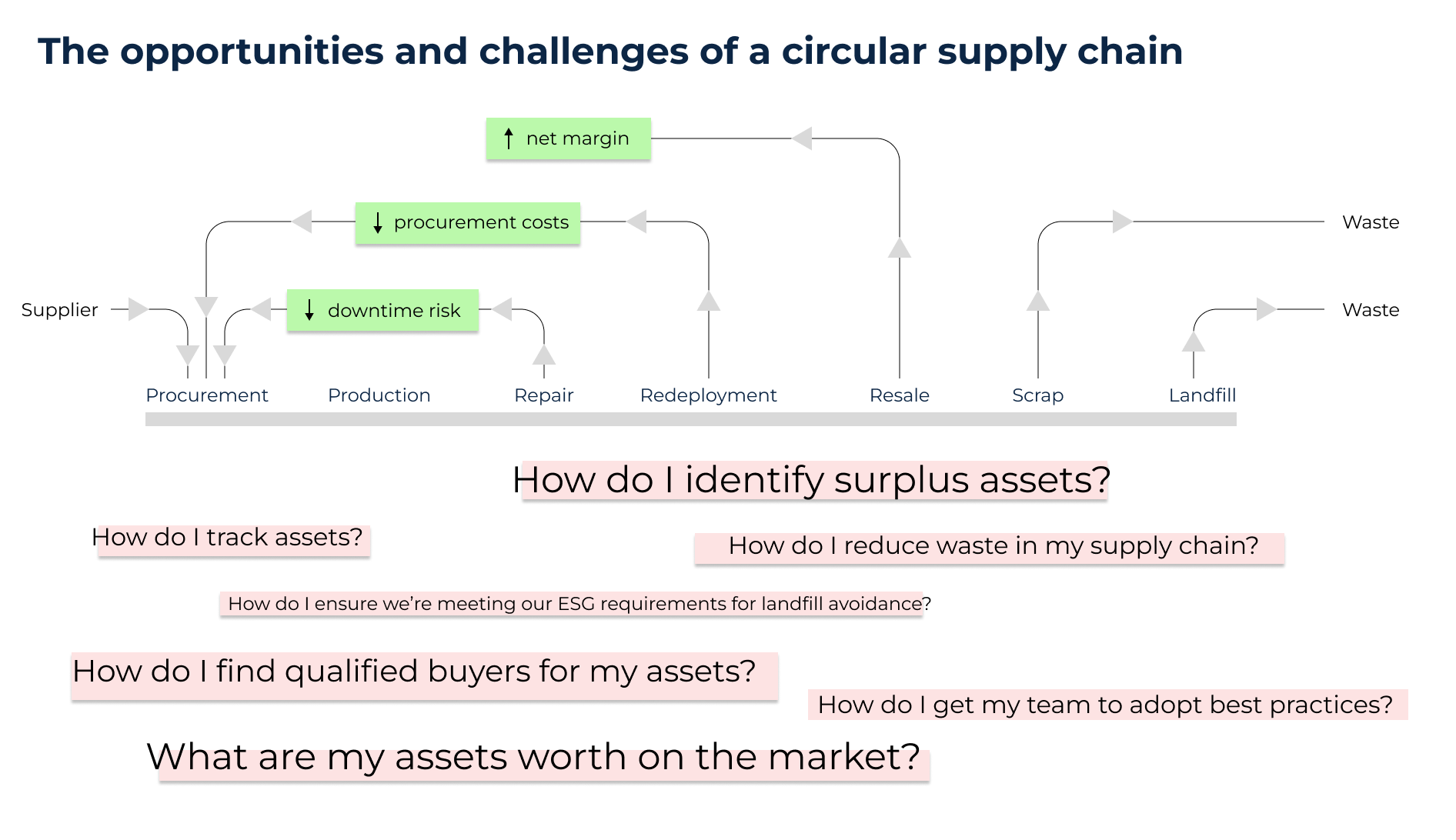
As investor and consumer pressure builds, executives in turn increase the pressure on their supply chain and operations managers to find solutions. The expectation is that instead of simply scrapping or landfilling items, asset managers should:
- Identify underutilized assets
- Gain approvals from appropriate stakeholders to write off these assets
- Attempt to redeploy these assets internally to other facilities
- Attempt to resell these assets on the second market (at fair market value)
- Do all of this without disrupting business as usual
This set of tasks gets increasingly complex as the size of the business increases, becoming nearly impossible to do well at the kind of scale at which most enterprise companies operate. Most of the asset managers that we meet have resorted to patching together different tools, paperwork, outside vendors and spreadsheets to try to make it all work.
The solution is (good) software, not more manual processes
There is no denying that industrial asset lifecycle management is a deep and complex problem. Solving it at enterprise scale requires improving asset visibility, coordination across teams, building repeatable and standardized processes, automating repeat workflows, and creating access to robust reporting mechanisms. In my experience, there is definitely a wrong and right way to address these issues. The wrong approach is to treat surplus asset management as an ad hoc problem to be solved whenever you run out of warehouse space; or when your CFO grumbles about rising inventory levels. Asset managers react by hiring a liquidator to sell whatever can be sold (typically at a fraction of the market value), and everything else gets hauled away to a scrapyard or landfill. This reactive approach is often extremely disruptive, creates risk and yields the lowest recovery on assets. The worst part is the business goes back to its old ways, repeating the cycle 12-18 months later.
After watching businesses struggle with asset management and destroy billions in asset value over the last 15 years, I am convinced that a small but important shift needs to be made in how industrial supply chains operate. Businesses procure assets on a regular and consistent basis. They also need to divest of unneeded assets in a similar fashion to maintain healthy balance sheets, inventory level, and to maximize their return on assets. Fortunately, this can be easily accomplished using a dedicated software solution that simplifies the process. A well thought out, enterprise ready software platform can standardize workflows, automate repeated tasks, simplify asset resale and provide real-time reporting on the entire process. This is why Aucto is launching ARS, a dedicated asset lifecycle management software built specifically to solve this problem.
Hopefully, I have made the case that it’s a problem worth solving. Businesses that have focused on improving their asset management processes self-report a 20:1 return on investment on a dollar basis, and a significant increase in landfill avoidance rates. It’s one of the few areas of businesses where you can directly quantify both the financial and environmental benefits of the effort.